Eddy current testing is a widely used non-destructive method for inspecting the integrity of metallic materials, including aluminium. In Egypt, the application of eddy current testing for aluminium has gained increased attention due to the growing demand for high-quality materials in various industries. This paper explores the current landscape of eddy current testing for aluminium in Egypt, focusing on the techniques and technologies being utilized in the country. A ndt laboratory comprehensive understanding of the use of eddy current testing for aluminium in Egypt is essential for ensuring the safety and reliability of aluminium components in industrial applications.
Exploring eddy current testing for aluminum in Egypt involves assessing the suitability of this non-destructive testing method for detecting defects and anomalies in aluminum components. This process typically involves using a coil to induce electrical currents in ndt companies near me the material, which generates a magnetic field that can be analyzed for variations caused by defects. The aim is to determine the effectiveness of this technique in the specific context of aluminum testing in Egyptian industrial applications, with potential benefits including improved quality control and reduced inspection times. This exploration may involve collaboration with local industry partners and research institutions to gather data and insights relevant to the Egyptian context.
Understanding Eddy Current Testing for Aluminium in Egypt
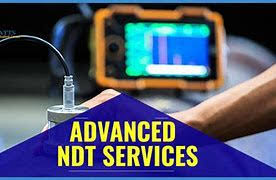
Understanding Eddy Current Testing for Aluminium in Egypt can help in the detection of surface and sub-surface flaws, such as cracks, corrosion, and other defects in aluminium components and structures. This non-destructive testing method is widely ndt non destructive testing used in various industries in Egypt, including aerospace, automotive, and construction, to ensure the integrity and safety of aluminium products. Eddy current testing is a quick and efficient way to inspect large volumes of aluminium components and can be performed on both ferrous and non-ferrous materials. It is essential for manufacturers and quality control professionals in Egypt to have a good understanding of eddy current testing techniques and equipment to maintain the highest standards of quality and safety in the production and use of aluminium materials.
The Benefits of Eddy Current Testing for Aluminium in Egypt
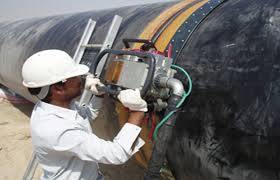
Eddy current testing for aluminium in Egypt offers a range of benefits, including non-destructive testing capabilities, high sensitivity to surface and near-surface flaws, and the ability to inspect a variety of shapes and sizes of components. This testing method is particularly advantageous for the aerospace and automotive industries in Egypt, as it can help ensure the safety and reliability of aluminium components used in aircraft, vehicles, and other critical applications. Additionally, eddy current testing is relatively fast and cost-effective, making it a practical choice for manufacturers and inspection companies in Egypt. Overall, the benefits of eddy current testing for aluminium in Egypt contribute to improved quality control and compliance with industry standards.
Eddy Current Testing: A Key Tool for Aluminium Inspection in Egypt
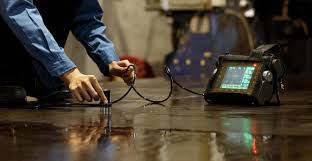
Eddy current testing is a non-destructive inspection technique that is commonly used for the examination of aluminum materials in Egypt. This method is particularly effective for detecting surface and near-surface defects in aluminum, such as cracks, corrosion, and variations in material thickness. The principle behind eddy current testing involves the use of an electromagnetic coil to induce eddy currents in the conductive material being inspected. Any disruptions in the material, such as those caused by defects, will alter the eddy currents and produce a measurable response. This enables inspectors to identify and characterize the defects without the need for physical contact with the material. In the context of aluminum inspection in Egypt, eddy current testing is essential for ensuring the integrity and quality of aluminum components used in various industries, such as aerospace, automotive, and construction. It provides a fast, accurate, and non-destructive means of assessing the condition of aluminum structures and components, helping to prevent potential failures and ensure compliance with industry standards. Overall, eddy current testing serves as a key tool for aluminum inspection in Egypt, providing valuable insights into the quality and reliability of aluminum materials and components. Its widespread application underscores its importance in ensuring the safety and performance of aluminum-based products in various sectors of the Egyptian economy.
The Role of Eddy Current Testing in Ensuring Aluminium Quality in Egypt
ndt laboratory
Eddy current testing plays a crucial role in ensuring the quality of aluminum in Egypt. This non-destructive testing method allows for the detection of surface and near-surface defects in aluminum materials, including cracks, voids, and discontinuities. By using eddy current testing, manufacturers can identify and address potential issues before the aluminum products are put into use, ensuring the safety and reliability of the final products. In the context of Egypt's aluminum industry, the use of eddy current testing helps to meet international quality standards and maintain a competitive edge in the global market. This technology has become an essential tool in the quality control process for aluminum production in Egypt.
Aluminium Quality Control in Egypt: Utilizing Eddy Current Testing
Aluminium quality control in Egypt is essential for ensuring the performance and reliability of the material in various applications. Eddy current testing is a widely used method for inspecting the quality of aluminium products. This non-destructive testing technique uses electromagnetic induction to detect surface and subsurface defects in the material. Eddy current testing is particularly effective for identifying cracks, corrosion, and material composition variations in aluminium products. It is also capable of providing accurate measurements of the thickness of protective coatings on the surface of the material. This method allows for fast and efficient quality control, reducing the risk of product failures and ensuring compliance with industry standards. In Egypt, the use of eddy current testing for aluminium quality control is becoming more prevalent as manufacturers and suppliers recognize the importance of delivering high-quality products to their customers. By implementing this advanced testing technique, businesses can improve their production processes, minimize waste, and ultimately enhance customer satisfaction.
Eddy Current Testing: A Necessity for Aluminium Manufacturers in Egypt
Eddy current testing is essential for aluminium manufacturers in Egypt because it enables them to detect surface and sub-surface defects in the material without causing any damage. This non-destructive testing method uses electromagnetic induction to identify flaws such as cracks, inclusions, and voids in the aluminium, ensuring that only high-quality products are delivered to customers. With the growing demand for aluminium in various industries, including construction, automotive, and aerospace, the need for reliable and efficient testing methods has become increasingly important. By implementing eddy current testing, aluminium manufacturers in Egypt can ensure the integrity and safety of their products, ultimately enhancing their competitiveness in the market.
Exploring the Effectiveness of Eddy Current Testing for Aluminium in Egypt
The effectiveness of eddy current testing for aluminum in Egypt is a topic of interest within the non-destructive testing (NDT) community. Eddy current testing is a non-destructive technique commonly used for inspecting conductive materials such as aluminum to detect surface and subsurface defects. In Egypt, where aluminum is widely used in various industries including construction, transportation, and manufacturing, the effectiveness of eddy current testing is crucial for ensuring the quality and safety of aluminum components and structures. Research and studies are being conducted to explore the application and reliability of eddy current testing for aluminum in the Egyptian context, with a focus on optimizing inspection procedures, equipment performance, and data analysis techniques. The findings from these efforts will contribute to enhancing the reliability and efficiency of eddy current testing for aluminum in Egypt, ultimately supporting the integrity and quality assurance of aluminum products and infrastructure in the country.